The Casting Process
1 Wax Injection
The investment casting process begins with the production of heat disposable wax patterns. The patterns are made by injecting wax into a metal mold. These disposable patterns are the same as the finished part but with allowances made for shrinkage.
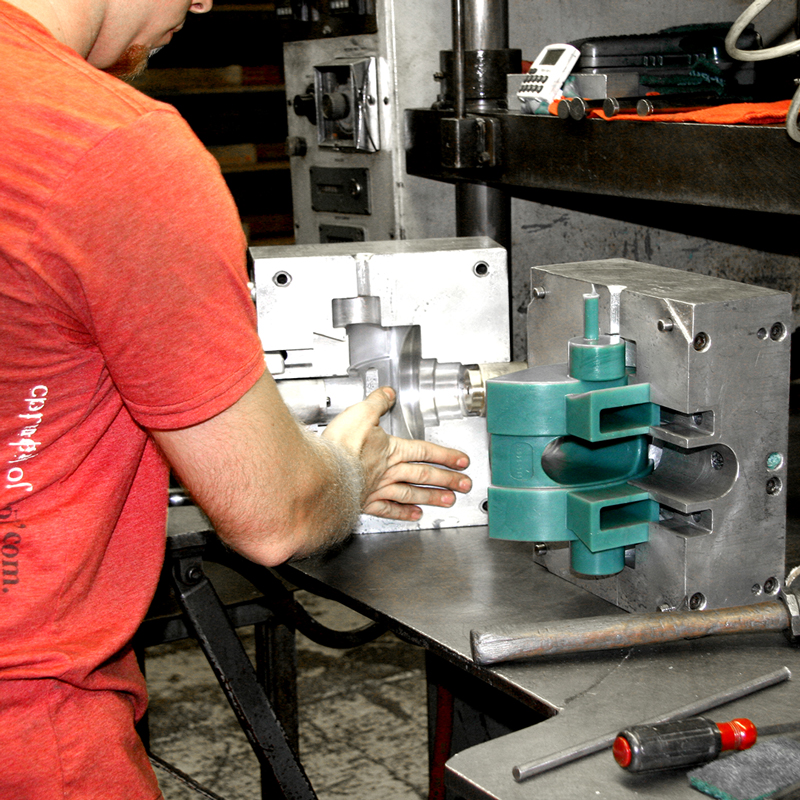
2 Pattern Assembly
Each wax pattern carries a gate. The gate has three basic functions:
- To attach patterns to a tree, forming a cluster.
- To provide a channel for draining out wax from the cluster.
- To provide a channel through which the molten metal will enter and feed the casting.
The wax patterns are fastened by the gate to runners, which is attached to a pouring cup. The patterns, tree and pouring cup form the cluster, commonly known as a tree, which is needed to produce the ceramic mold.
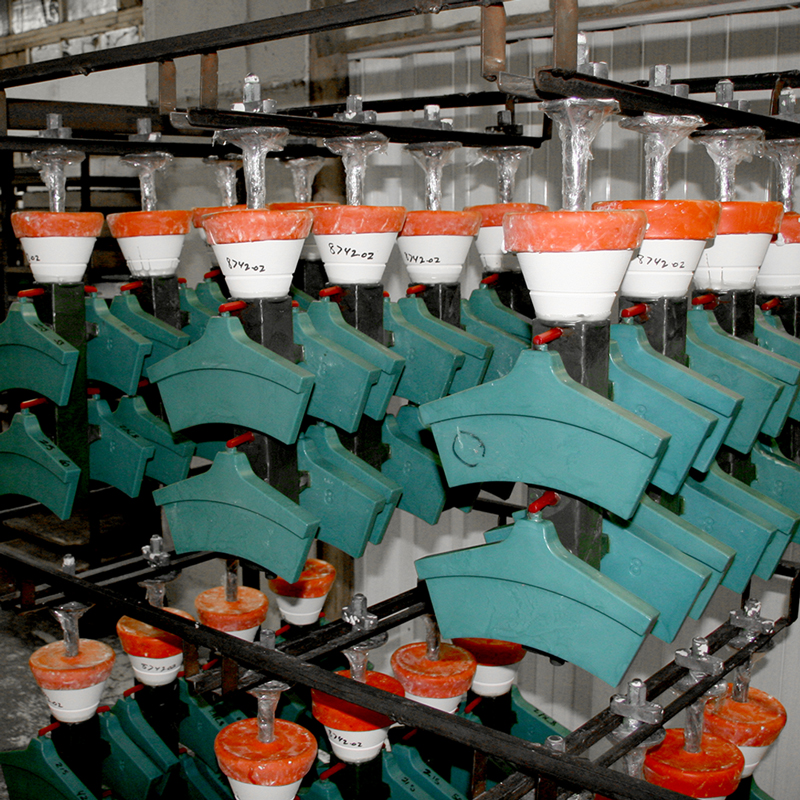
3 The Shell Process
The ceramic shell mold technique involves dipping the entire cluster into a ceramic slurry, draining it and then coating it with a fine ceramic sand. After drying (in a humidity and temperature controlled environment), this process is repeated again and again, using progressively coarser grades of ceramic material, until a self supporting shell has been formed.
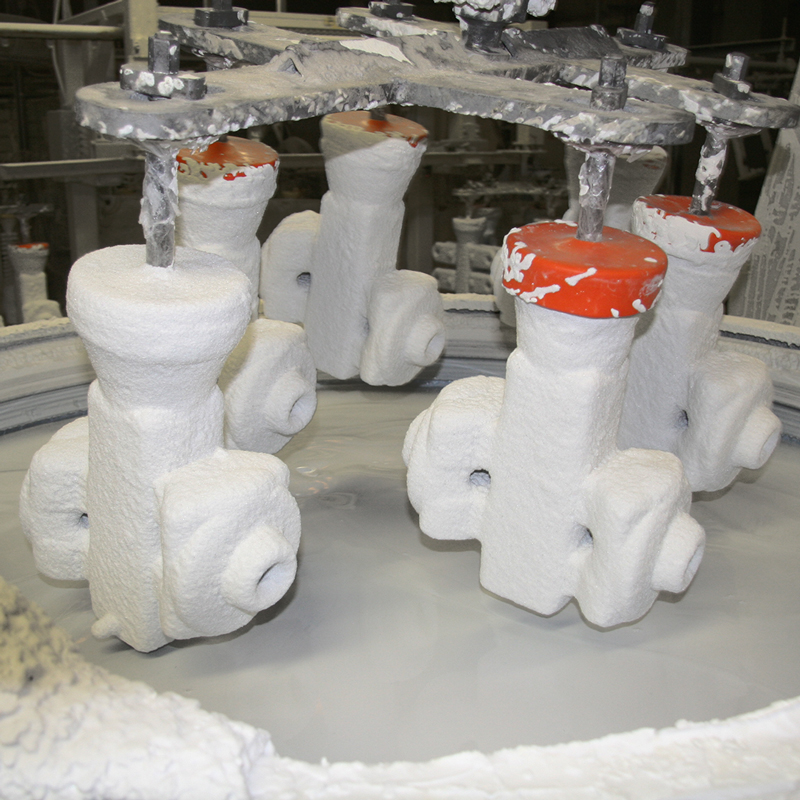
4 Dewax
The ceramic shell is placed in a high temperature steam autoclave where the wax will melt out of the shell. This will leave a ceramic shell containing cavities of the desired casting shape along with the designed running and feeding system.
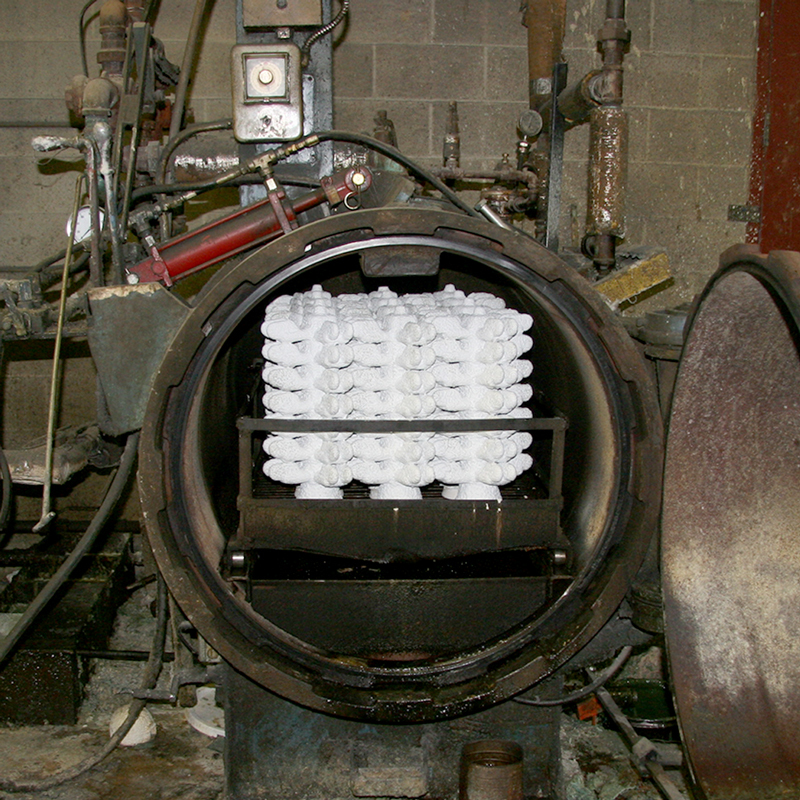
5 Casting
The ceramic shell is fired to burn out the last traces of wax, as well as to develop the high temperature bond of the ceramic system and to preheat the mold in preparation for casting. Gravity is utilized to pour the molten metal into the fired ceramic shell.
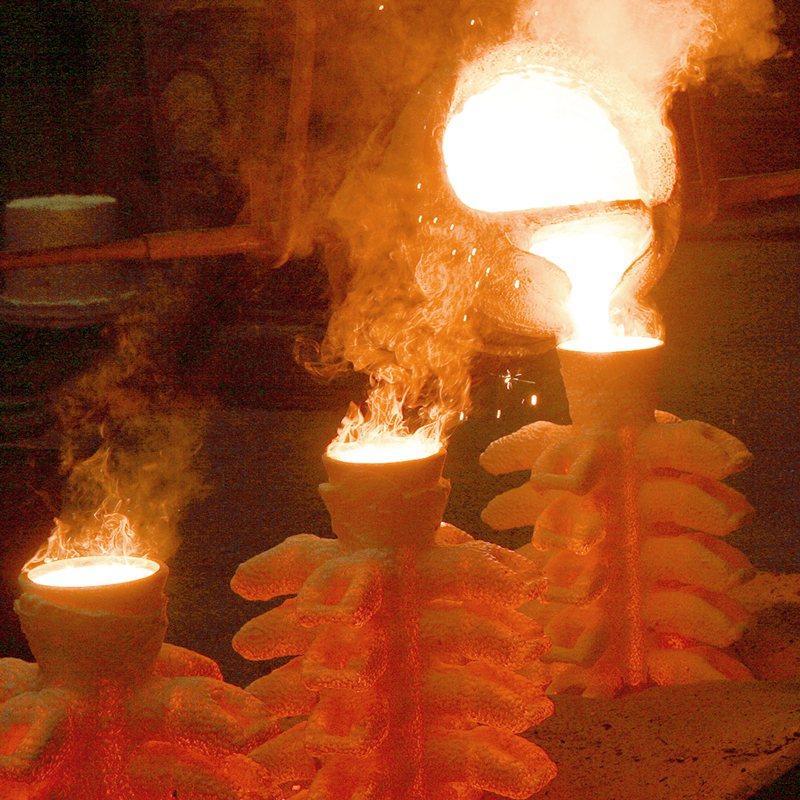
6 Cleanup
After the poured molds have been cooled, the mold material is removed from the cluster. This is done by mechanical vibration and chemical cleaning. Individual castings are then removed from the cluster by means of friction saws and cut-off wheels. Any remaining protrusions left by gates are removed by gate grinding.
The castings are now ready for any secondary operations such as heat treating, straightening, machining and for whatever inspection is specified.
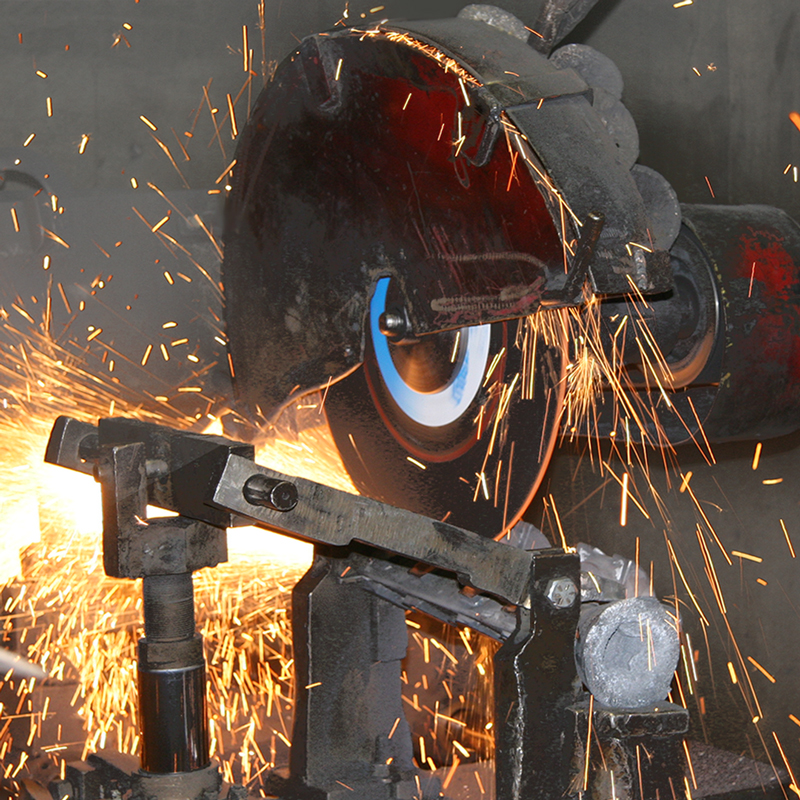